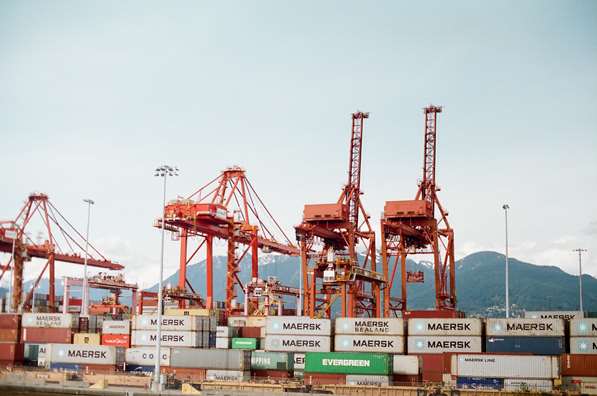
As lockdown continues, construction on-site productivity is predicted to fall by 12% if current conditions persist, according to the Royal Institution of Chartered Surveyors.
These conditions are largely defined by the availability of supply and labor. With most of the world’s workforce having to work remotely, an option not available for construction, the industrial industry finds itself at a significant disadvantage. Let’s take a deeper look at the factors surrounding this issue.
Major Supply Chain Deficiency Rooted In China
The pandemic’s main impact on the construction industry stems from a disruption of the supply chain. In particular, the deprivation of Chinese material imports has had the most significant impact on import-dependent firms. US construction firms, for example, depend on China for a substantial amount of their construction materials. These materials range from raw materials such as steel, aluminum, and other metals, to decorative materials such as stone ornaments.
According to recent estimates, the least dependent US firms rely on China for 30% of their materials, while some go as high as 80%. Import figures are predicted to shrink even further as the pandemic progresses. As a focused example, the shutdown of material manufacturers in China will lead to a projected 23 percent year-over-year reduction in material imports in the port of Los Angeles alone. This supply drought, coupled with lack of demand, is causing construction firms US-wide and abroad to experience the most significant industry dry spell in recent history.
Effects And Adaptations In Supply And Labor
At present, a few Chinese manufacturers have resumed production, with more preparing to follow suit. However, their staffing at the moment is only a fraction of what it once was. These skeletal workforces are clamoring to serve the extensive queue of orders that have been put on hold since the beginning of 2020. Several price hikes have been recorded for raw materials as well as manufactured goods such as construction equipment spare parts. As a result of these circumstances, more US firms have begun to look into local suppliers to buy parts for construction equipment, materials, and other such supplies.
The shutdown of non-essential labor has impacted the construction industry significantly as well. In areas where lockdown is in full effect, even essential government construction projects are operating with only half their full workforce. This number is further curtailed by the fact that some employees live in high-risk areas and are banned from traveling. This is an issue for which no workaround has yet been found. The lack of skilled labor will inevitably cause some projects to be put on hold entirely.
Far-Reaching Economic Impact
The severity of the impact on the construction industry has had some far-reaching effects on the global economy. Delays in construction will inevitably hamper economic recovery, and investors are already anxious about these setbacks. The US stock market experienced one of its greatest blows since 1987 early in 2020 and has been struggling to bounce back since. The World Bank has speculated that the combined economic impacts of COVID-19 can lead to a worldwide recession that can last until 2022.
This estimate lines up with a statement from Anirban Basu, a chief economist for Associated Builders and Contractors. In the statement, he put the economic recovery setbacks caused by construction delays at 12 to 18 months. Project cancellations could lead to an increased availability of labor and materials and pave the way for an economic rebound. However, this means that the economy will further decline before it can work towards recovery.
The increasingly dire situation for the construction industry makes the need to relax lockdown strictures and create a cure for COVID-19, even more pressing. Fortunately, however, local suppliers are working tirelessly to ensure that what construction projects are allowed to operate never run out of materials.